Chinese Awards Manufacturer
At our on-site workshops, MC ART AWARDS is committed to the design and production of customized awards. Leveraging state-of-the-art technology, advanced techniques, and high - quality materials, we ensure a flawless finish for every award, consistently meeting the highest standards of craftsmanship.

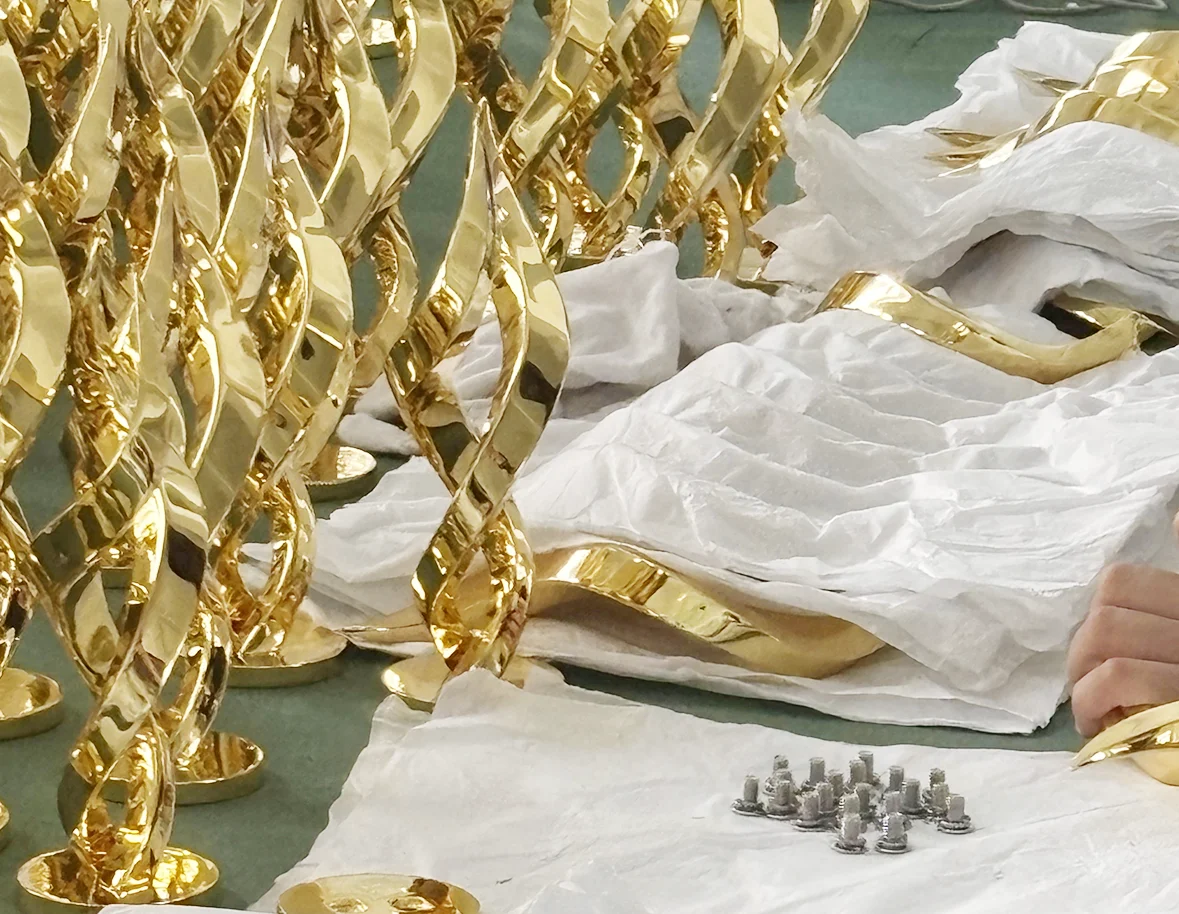
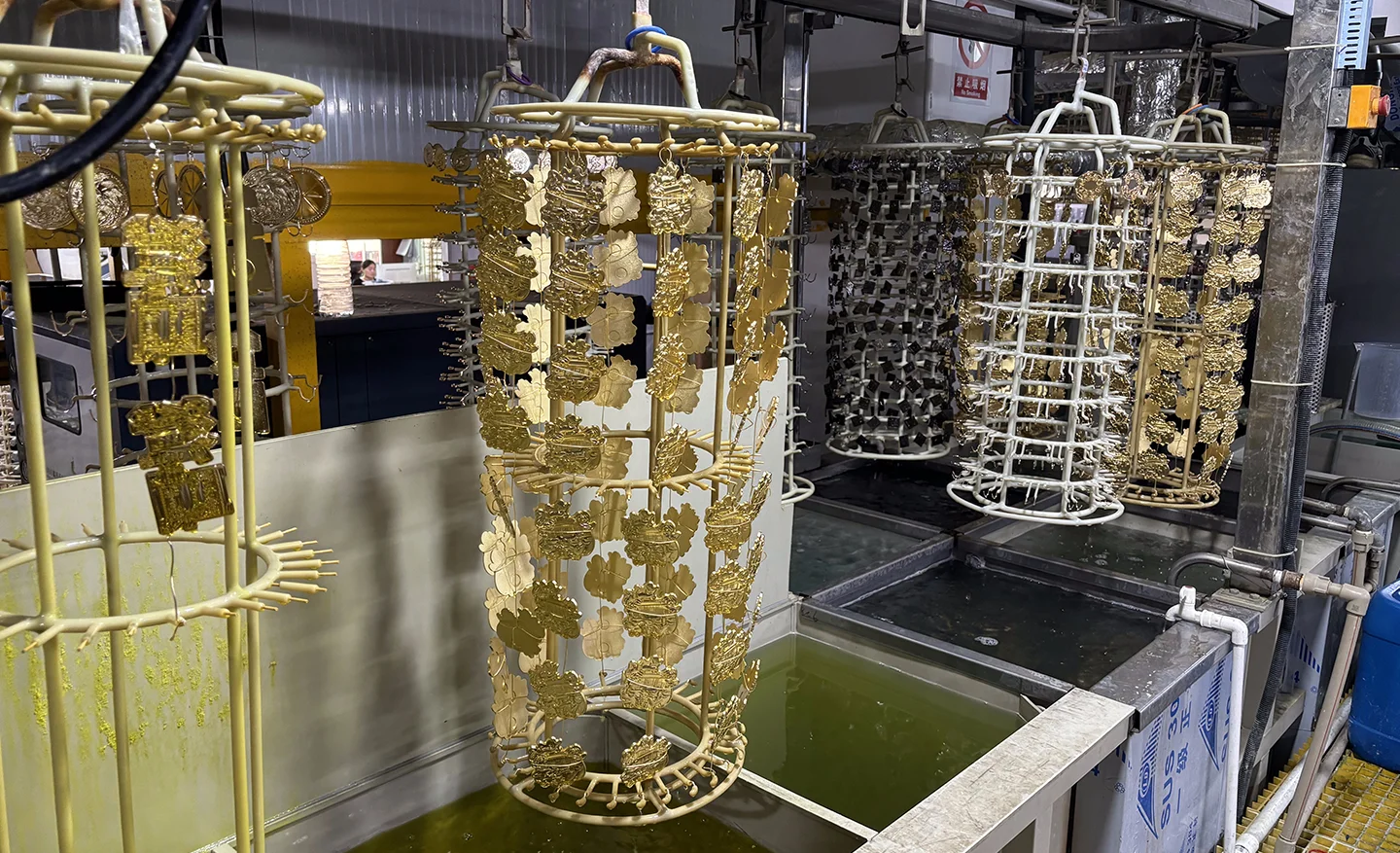

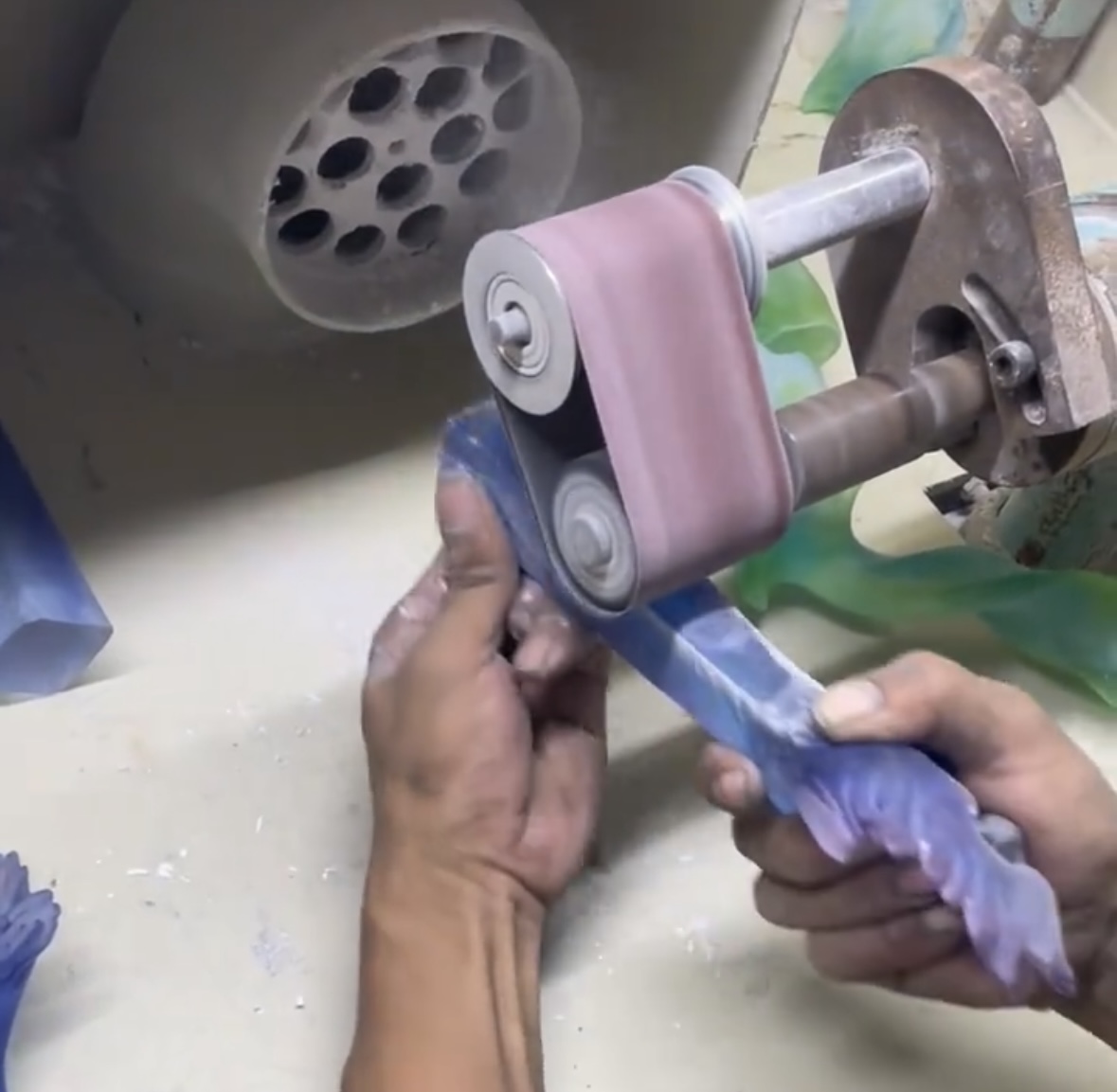
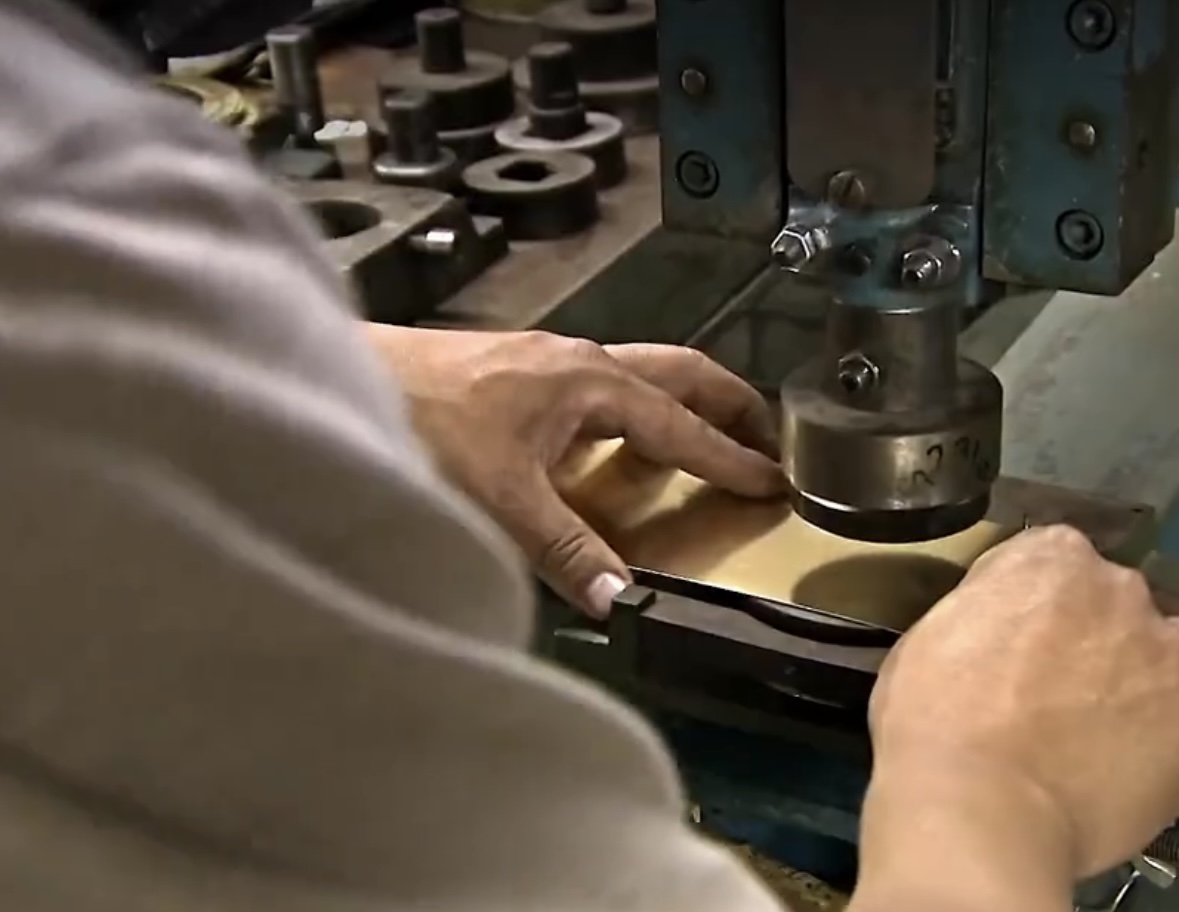
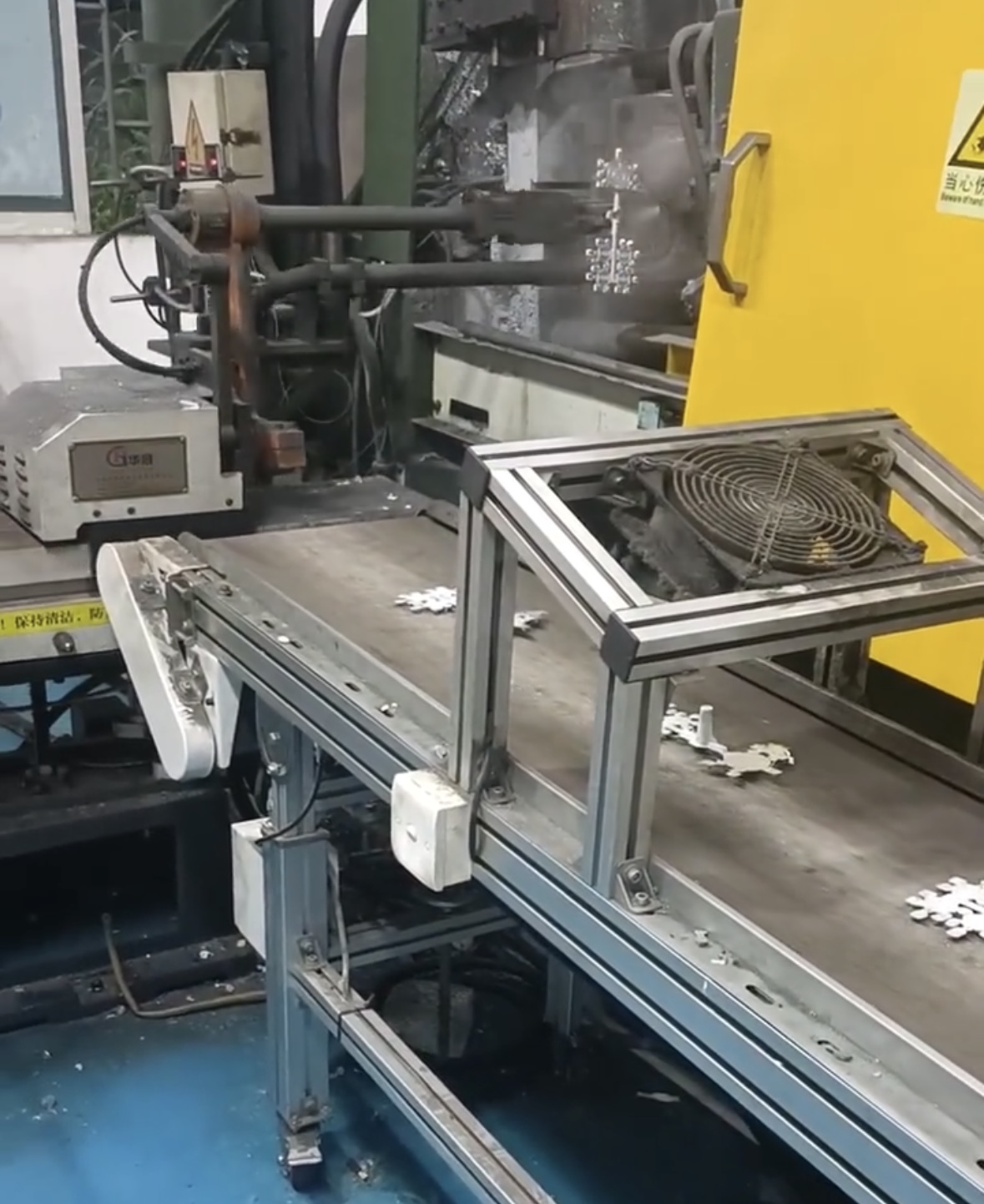
How it works
Awards making process
MC ART AWARDS conducts all manufacturing operations in - house at our factory located in Shenzhen, China. This vertically integrated approach empowers us with comprehensive control over every facet of the service we deliver to you.
We make substantial investments in procuring the finest tools, cutting - edge technology, and advanced machinery. These resources are harnessed to ensure the production of awards and trophies of the utmost quality.
At MC ART AWARDS, we hold our work in high regard and derive significant pride from it. Owning an on - site trophy manufacturing process not only enables us to offer enhanced flexibility in our service but also ensures that we can rapidly adapt to your specific requirements, guaranteeing a seamless and personalized experience for all your award - related needs.
We make substantial investments in procuring the finest tools, cutting - edge technology, and advanced machinery. These resources are harnessed to ensure the production of awards and trophies of the utmost quality.
At MC ART AWARDS, we hold our work in high regard and derive significant pride from it. Owning an on - site trophy manufacturing process not only enables us to offer enhanced flexibility in our service but also ensures that we can rapidly adapt to your specific requirements, guaranteeing a seamless and personalized experience for all your award - related needs.
Finish Options
We offer a wide range of finishes and finishes to suit all events and occasions. Below we show you some of the more basic finishes. If you have another finish idea, please contact us.
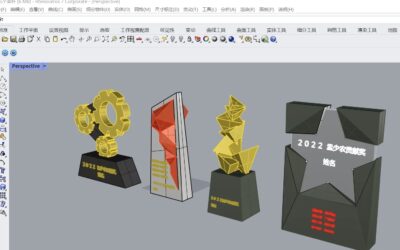
2D and 3D Design
2D and 3D Design: Graphic design software is used for 2D graphics of product appearance and layout, while 3D modeling software constructs 3D models. The former provides a production blueprint, and the latter enables full - view display and detailed adjustments of product shapes.
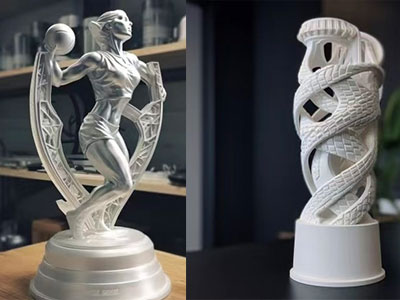
3D Prototyping Printing
3D printers stack materials layer - by - layer following 3D model data to quickly make product prototypes for design verification.
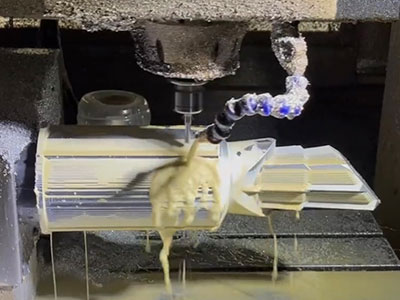
CNC Engraving
CNC controls machine tools with digital programs, precisely cutting materials to make complex - shaped parts with high precision.
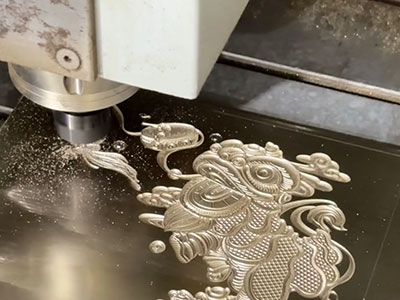
Mold Manufacturing
Molds are made according to product designs and used for mass - producing identical - shaped products, improving efficiency and consistency.
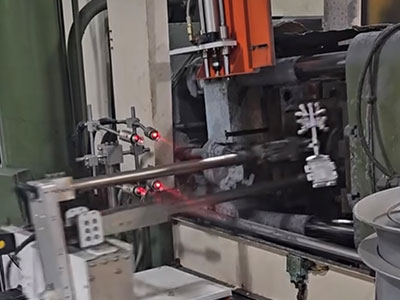
Die - Casting Molding
Liquid metal is injected into mold cavities under high pressure and solidifies to form products, suitable for complex metal parts.
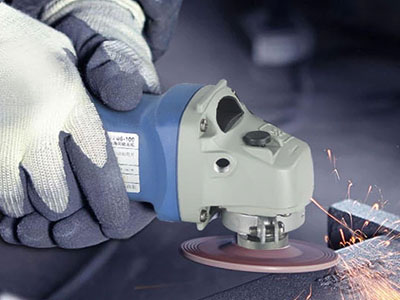
Polishing and Grinding
This process removes surface defects to make the product surface smooth, enhancing appearance.
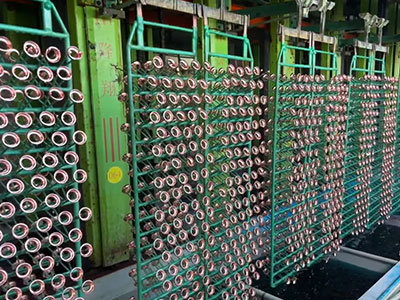
Electroplating coloring
Electroplating deposits a metal layer on the product surface and can add color, improving decoration and corrosion resistance.
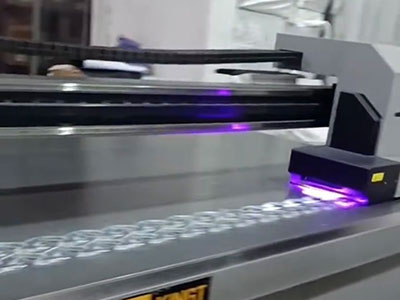
UV Printing
UV - curable inks are printed on the product surface by a press, curing fast with vivid and durable colors.
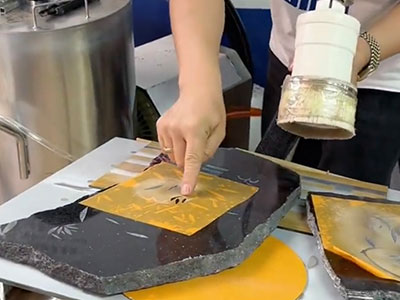
Sandblasting lettering
Compressed air sprays abrasive materials onto the product surface at high speed to create engraved marks, increasing surface texture.
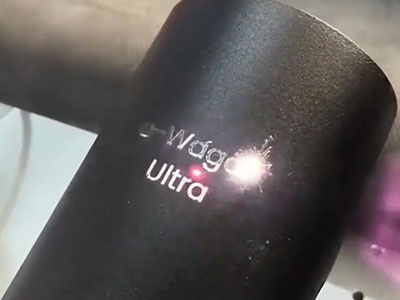
Laser Engraving
High - energy laser beams burn permanent text or patterns on the product surface with high precision.
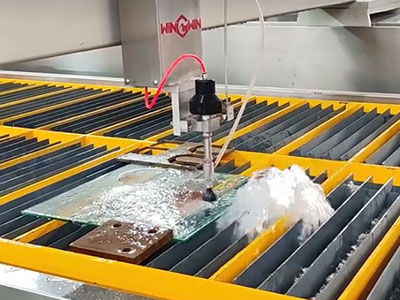
Waterjet Cutting
High - pressure water jets with abrasives cut materials into complex shapes with little damage.
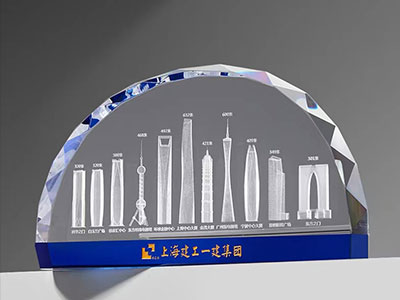
3D Laser
3D crystal laser engraving uses high - energy lasers. The laser passes through the clear crystal and focuses precisely at specific internal spots. By inducing small fractures or structural changes at these points, 3D images or patterns are crafted inside the crystal.